by Keith Yoerg (RRS Secretary)
The latest meeting of the Reaction Research Society took place Friday, July 9th and had 15 attendees who came and went – all members. We kicked off the meeting chatting about various items, including the news that Relativity Space (a 3D-Printed rocket engine company led by 2 USC Rocket Propulsion graduates who have tested rockets at the MTA) has just signed a contract for a building in Long Beach.
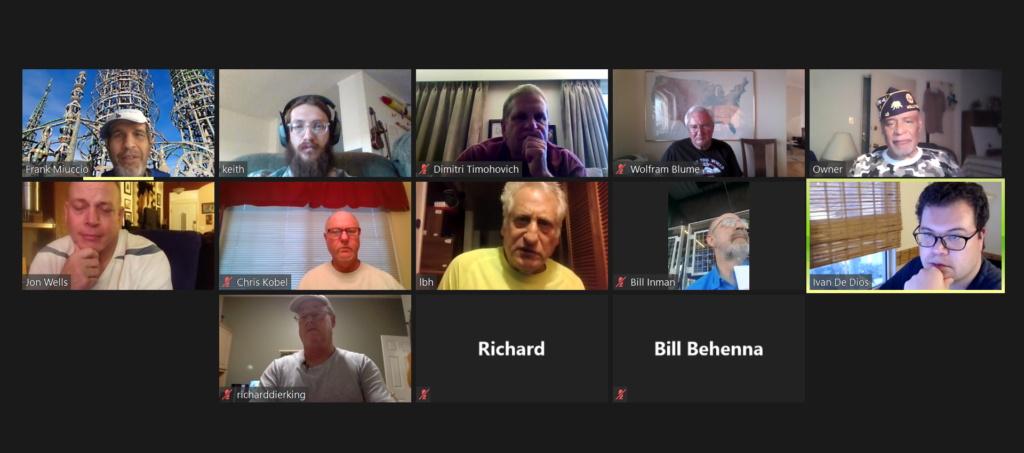
RICHARD BUTTERFIELD REMEMBERANCES
The RRS received sad news of the passing of an extremely devoted and well liked member – Richard Butterfield. Richard became a member of the RRS in the 1950s, and was heavily involved in recruiting new members for the organization while he lived in Long Beach working for a local aerospace company. Eventually, he moved out to the Mojave Desert at some land to the northwest of the MTA. Following a fire at his property which destroyed his workshop & part of his house he moved back into town.
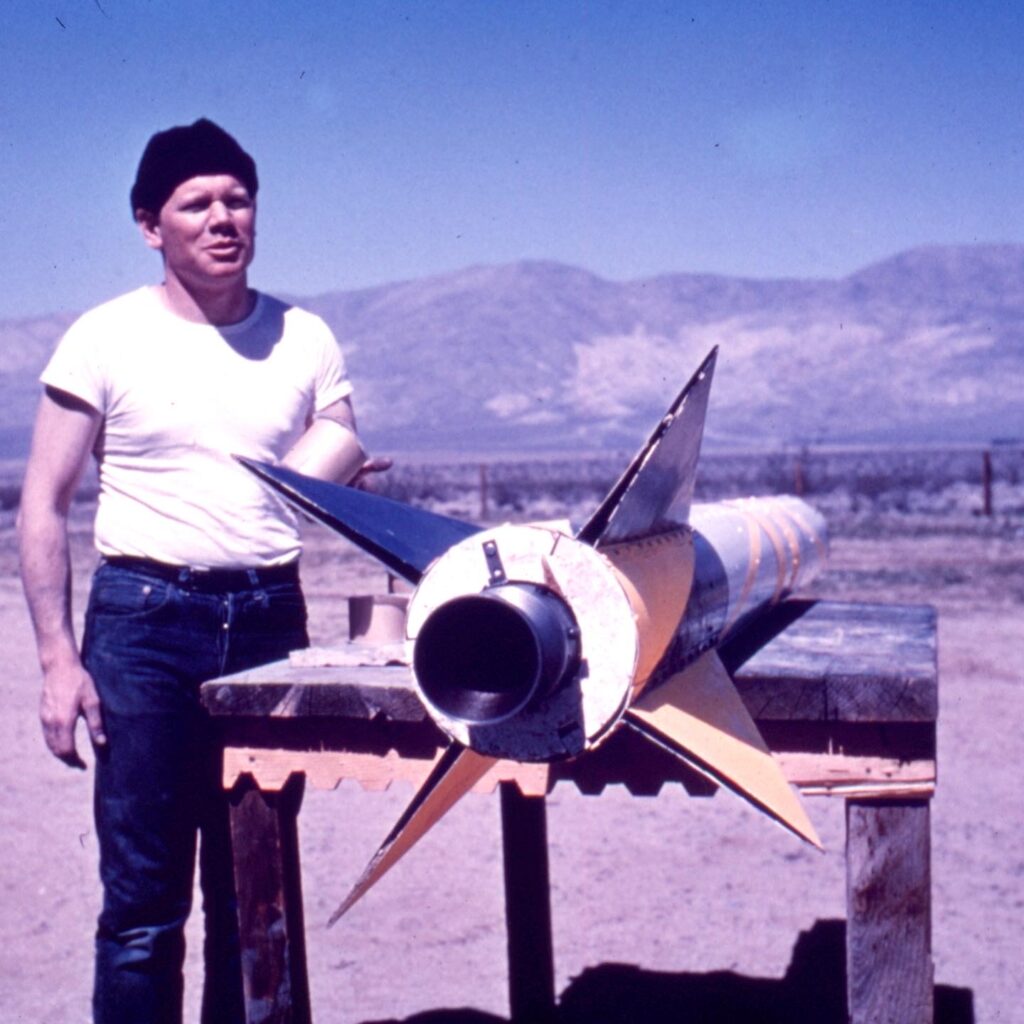
Several members who knew Richard shared their remembrances and stories of Richard, recalling that he was always very welcoming to those new to the hobby. All spoke very highly of him. We intend to compile a more formal collection of stories (and photos) to pay proper tribute to this great man.
MTA PERMANENT BATHROOM UPDATE
Progress is continuing on the permanent RRS Bathroom structure. A 20-foot shipping container has been purchased and work is being done to cut out areas for doors and ventilation windows. That work is expected to be completed within the next week or 2, at which time the container will be delivered to a hangar of RRS member Wilbur Owens for the next stages of construction including adding plumbing, fixtures, and the doors and windows. See below for a schematic of the current plans for the bathroom.
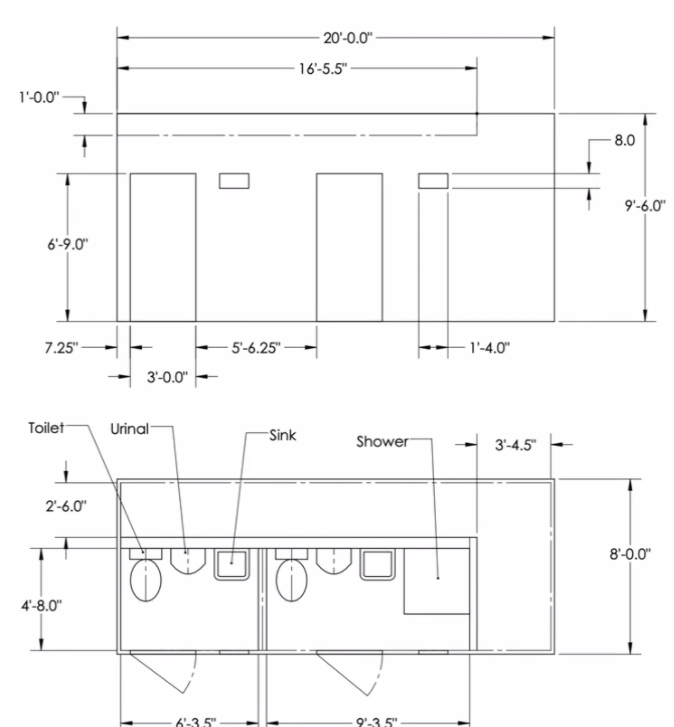
The bathroom conversation opened a discussion on other MTA site improvements that members would like to see – including solar power solutions, firefighting (possibly via a Kowasaki mule or similar ATV), and sun-protection behind the Dosa building. While the bathroom is the top site improvement priority, these other improvements are an important part of providing a world-class location for amateur rocket enthusiasts to conduct their activities.
AMAZON SMILE DONATION
The RRS received $23 in donations as a result of members and others using smile.amazon.com when ordering online – and selecting the Reaction Research Society as the charity to benefit. Thank you to all who have helped with this contribution, it should help us celebrate when we can finally have our monthly meetings in-person once again (pizza party anyone?).
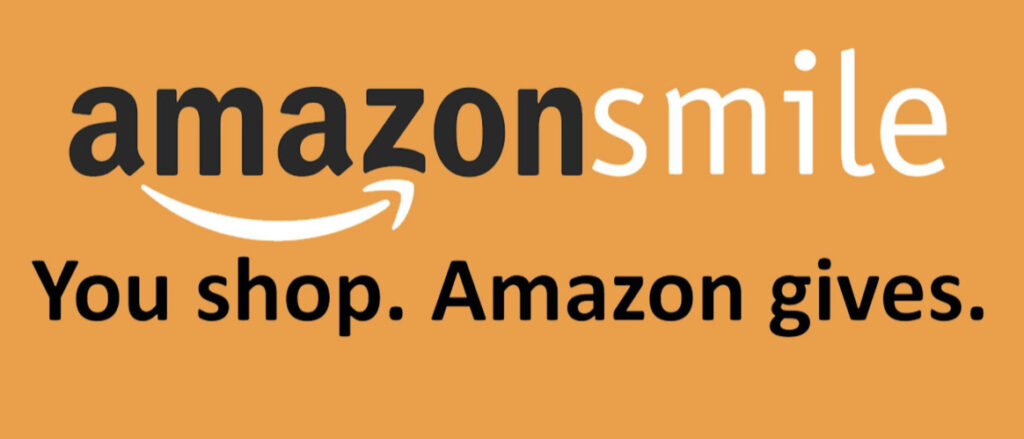
IN-PERSON MEETINGS IN GARDENA
While the City of Gardena does not have concrete plans on when they may re-open the Ken Nakaoka Community Center – they have informed us that it will be the last thing that is going to open. It sounds like Gardena is taking a very cautious approach, and intends to see how opening the parks goes first and then move from there. While we don’t know for sure – the hope is that we may be able to host an in-person meeting in September. Members will be informed via the monthly meeting invite once meetings will be allowed in person again.
Out of town members (temporary or permanent) don’t need to worry – we will continue to provide a zoom component for our meetings to allow those members to join. We have several members who have been very dedicated to meetings but would have trouble making it in-person & we want to keep everyone engaged! Not to mention it makes guest presentations from colleges and other groups from around the country much easier.
CLASSES & COMMUNITY OUTREACH
Frank has been working diligently to set up classes to get back to our community outreach of getting the local youth exposed to & excited about rocketry. The goal is to teach out of the Strive learning facility in Watts, which has been providing a space for local at-risk youth to expand their horizons for over 30 years. We pan to teach the classes on Wednesdays in September – and then taking the kids for a launch day at the MTA in early October.
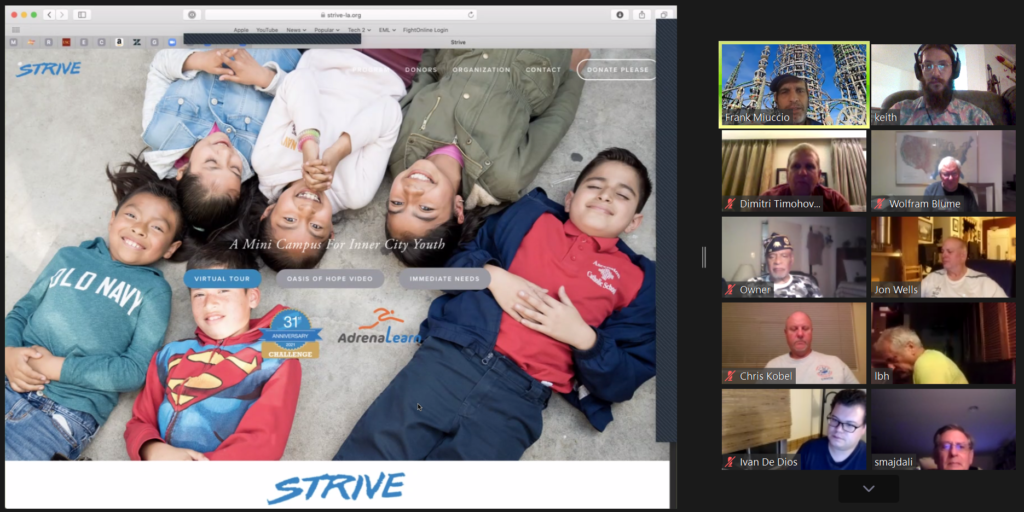
Any members interested in assisting the teaching of these classes can reach out to Frank at: vicepresident@rrs.org.
NEXT MONTHLY MEETING
The next RRS monthly meeting will be held virtually on Friday, August 13th at 7:30 pm pacific time. Current members will receive an invite via e-mail the week of the meeting. Non-members (or members who have not received recent invites) can request an invitation by sending an email to:
secretary@rrs.org
Please check your spam folders and add secretary@rrs.org to your email whitelist to make sure you receive the invitation.